Introduction: Darrieus Wind Turbine
Our team created a wind powered generator in the form of a Darrieus Vertical Axis Wind Turbine. Our aim was to create a turbine which generated as much power possible using motor in a wind tunnel. We also needed to design the wind turbine with a specific market in mind. We decided that our turbine would be suited best to educate children about the environment and renewable energy.
Nessessities for this project.
Materials:
4 Pieces of 550 x 350 x 15 MDF
Steel rod (440x (diameter 19)
15 bore ball bearings (high quality bearings used in bike hubs)
4M threaded aluminuim rod
6mm thick clear acrylic (required for gear)
3500RPM motor generator
Joints:
Tools:
bandsaw
power drill
sand paper
lathe
disc sander
Step 1: Blades
1) We carried out research and decided that 2 symmetrical aerofoil blades would suit our needs best. We used this website http://www.ae.illinois.edu/m-selig/ads/coord_database.html and selected the NACA 015 aerofoil section template.
2) Using this file, we then created a model in solid works. This was a 2D representation of the NACA 015.
3) We then placed the file in Adobe illustrator and laser cut the shape out of 6mm thick clear acrylic. This was then used as a guide/template.
4) Each blade consists of 2 pieces of 18mm thick ( 80mm long and 320mm deep). PVA was used as an adhesive to stick each piece of MDF together.
5) The acrylic template was then used to draw the outline of the aerofoil section on each end of the MDF.
6) The belt sander was then used to sculpt each blade. The acrylic template was constantly used to check that the blade was being sanded correctly.
7) Finally, each blade was varnished and sanded 6 times to gain a very smooth finish.
Step 2: Central Axle / Horizontal Rods
Central Axle
1) We used a steel rod as our central axle.
2) Dimensions: 440mm x 19mm (diameter).
3) To reduce weight, we hollowed out the top half of the rod. Using a 15mm bore drill.
4) 2 4mm holes were drilled 280mm apart to cater for the horizontal rods.
5) The rod was stepped at the bottom. 80mm at the bottom of the rod was machined down to 15mm(diameter). This was carried out so the rod would fit our bearings. Also, it was stepped so it sat on the top bearing.
Horizontal Rods
1) 2 threaded (4M) rods were used to attach the blades to the central axle.
2) Rods were 280mm long.
3) They were secured using nylon self-locking nuts on either side of the axle. Nylon locking nuts were also used to secure the blades.
Step 3: Gears
As our turbine had a large amount of torque, we felt that it would be beneficial to have a large gear ratio.
1) We designed an 80 tooth gear (80mm diameter) on solidworks and laser cut it using 6mm thick acrylic.
2) We made our own coupling out of steel, it was machined on the metal lathe.
3) This then meant that we could secure it to the central axle, avoiding slip.
Step 4: Base/Motor.
1) Base was essentially based on a 2 tier cake. 4 Pieces of 550 x 350 x 15 MDF were used. Using PVA, 2 pieces were glued to create one tier.
2) Each tier was separated using 6 pieces of pine, spacing the top and bottom tier by 50mm.
3) As shown in the picture, we cut out a slot for the motor (large slot is 57mm wide. 2 smaller slots are 5mm wide (for bolts to secure motor)). We did this so gear ratios could be altered. If the used wished to change the gear ratio, the motor could be moved closer or further away from the central axle.
4) We created holes in a piece of sheet steel for the motor. This allowed us to firmly secure the motor to the base.
Step 5: Bearings/ Sleeve
Apologies, this step will not be explained well as we do not have photographs of the individual pieces.
1) The top tier of the base was drilled through completely using a 35mm fostners bit. This fit one bearing. The axle sat on this bearing.
2) the bottom base was drilled half way through using a 35mm fostners bit. This created a step for the bearing to sit on. (a 20mm hole was drilled all the way through to let the axle float).
3) Each bearing was separated using a steel sleeve. The sleeve was 35mm in diameter. This is pictured.
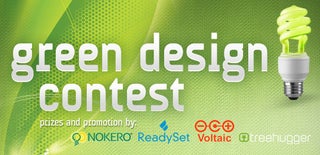
Participated in the
Instructables Green Design Contest